Seamless pipes, otherwise known as SMLS (seamless pipe) have become a staple of the industrial world. With their increased production and benefits to industries, they are becoming increasingly important for businesses everywhere.
Seamless pipes bring about improved efficiency in production processes, better durability, and safety standards while providing more reliable results for end-users. Through advanced technology, companies can now produce seamless pipes quickly and cost-effectively without compromising on quality.
This article will explore the production process behind seamless pipes, and discuss their many benefits and their relevance in various industries today.
Manufacturing of Seamless Steel Pipes
The manufacturing of seamless steel pipes is a complex process that requires precision and expertise. It involves the use of highly specialized machinery to produce pipes of consistent sizes, shapes, and lengths.
The most common method used for producing seamless steel pipes is by hot rolling or cold drawing. Hot-rolled pipe involves heating the metal until it reaches a temperature suitable for shaping into the pipe while cold-drawn pipe involves using dies to draw the heated material through an extrusion die to shape it into a desired form.
Depending on customer requirements, various processes may be employed to refine the raw material further such as cutting off excess length or threading one end of the finished product. The combination of these processes results in superior quality products with greater durability than welded steel pipes due to their lack of seams and improved mechanical properties resulting from being produced from solid homogenous material stock.
In addition, they are often preferred over welded alternatives due to their ability to be easily routed without having any sharp corners which can potentially cause fluid flow disruptions when navigating piping systems. Furthermore, their long lifespan makes them attractive choices for industrial applications where longevity is important such as oil & gas pipelines carrying corrosive liquids or those exposed directly to harsh weather conditions like offshore rigs in marine environments exposed to salt water spray or desert environments subjected to high temperatures during summer months.
Overall seamless steel pipes provide great value in terms of performance and longevity making them an ideal choice for many industries including automotive construction, HVAC, plumbing, petrochemical engineering, power generation, and aerospace manufacturing. Their versatility allows them to accommodate different pressure ratings as well as critical safety requirements depending on application needs giving manufacturers another advantage when selecting materials needed for specific projects.
Advantages of Seamless Steel Pipes Industrial
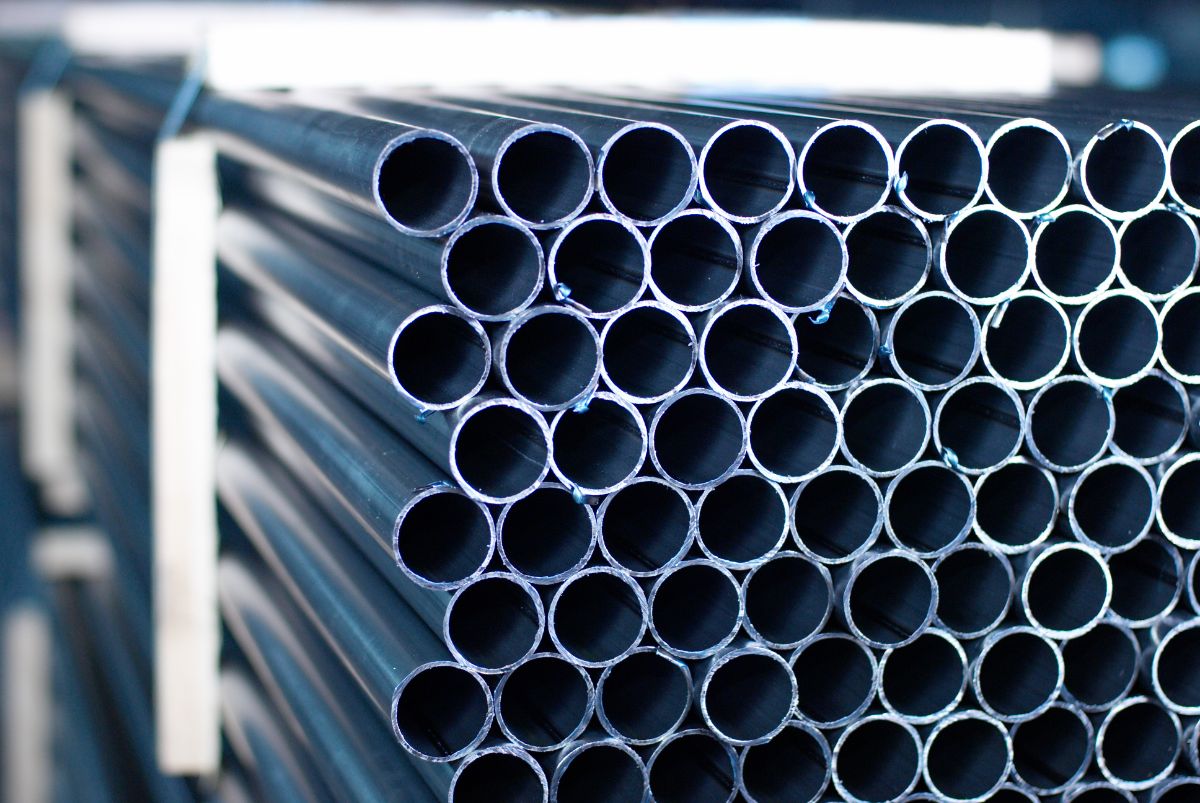
Seamless steel pipes are metal pipe that is manufactured without any seams or welds. This type of industrial piping has many advantages over its traditional counterparts that make it an ideal choice for an array of industries.
The most notable benefit to using seamless steel pipes is their strength and durability, as they are much less likely to corrode or break down than other types of pipes due to their lack of seams. Additionally, seamless steel pipes can be custom-fitted to meet the exact needs of any given industrial application, providing flexibility and convenience when it comes to installation.
Furthermore, they have a lower risk for leaks due to their lack of a seam which increases safety while also reducing maintenance costs over time. As such, seamless steel pipes offer numerous benefits in production efficiency and cost savings compared to other types of piping materials available today.
Role of Seamless Steel Pipes in Industrial Applications
Seamless steel pipes are increasingly becoming the choice of material for a variety of industrial applications due to their numerous advantages. Seamless pipes can be used in low- and high-pressure applications, as well as extreme temperatures while providing superior strength and resilience compared to traditional piping materials.
Due to its durability and resistance to corrosion, seamless steel pipe is often the preferred option for transporting fluids or gases over long distances. Additionally, these pipes provide greater flexibility when it comes to assembly since they do not require welding or other forms of joining.
This makes them ideal for complex systems where multiple components need to be connected securely without compromising on quality or performance. Furthermore, seamless steel pipes have superior fatigue life which makes them suitable for repeated loading cycles in heavy machinery such as pumps or compressors.
All these factors make seamless steel pipes an invaluable component in various industrial settings that demand reliability and robustness from their equipment components.
Conclusion

Seamless pipes are a popular choice among industrial professionals due to their production process, benefits, and relevance to the industry. Seamless pipes are made through an extrusion process that creates one continuous piece of pipe from a solid steel billet.
This results in fewer weld points, making them incredibly strong and more cost-efficient than other piping options like ERW pipe. Additionally, seamless pipes offer increased corrosion resistance and greater durability compared to ERW pipes.
These features make them ideal for use in high-pressure applications and extreme temperature environments. All in all, seamless pipelines have become increasingly important for industries needing reliable strength combined with affordability over time; they are sure to remain relevant as advancements continue.