FR-4 is one of the most widely used materials in the world for printed circuit boards (PCBs). Its superior thermal and electrical properties make it an ideal choice for engineers when designing and constructing circuits.
In this article, we will explore the basics of FR-4 material, from its composition to its applications. Well take a look at how FR-4 compares to other PCB materials and discuss why it’s so popular among professionals. Finally, we’ll examine some tips on using FR-4 for your projects.
By the end of this article, you’ll have a better understanding of what makes FR such an indispensable material in today’s electronic industry.
Introduction to FR-4
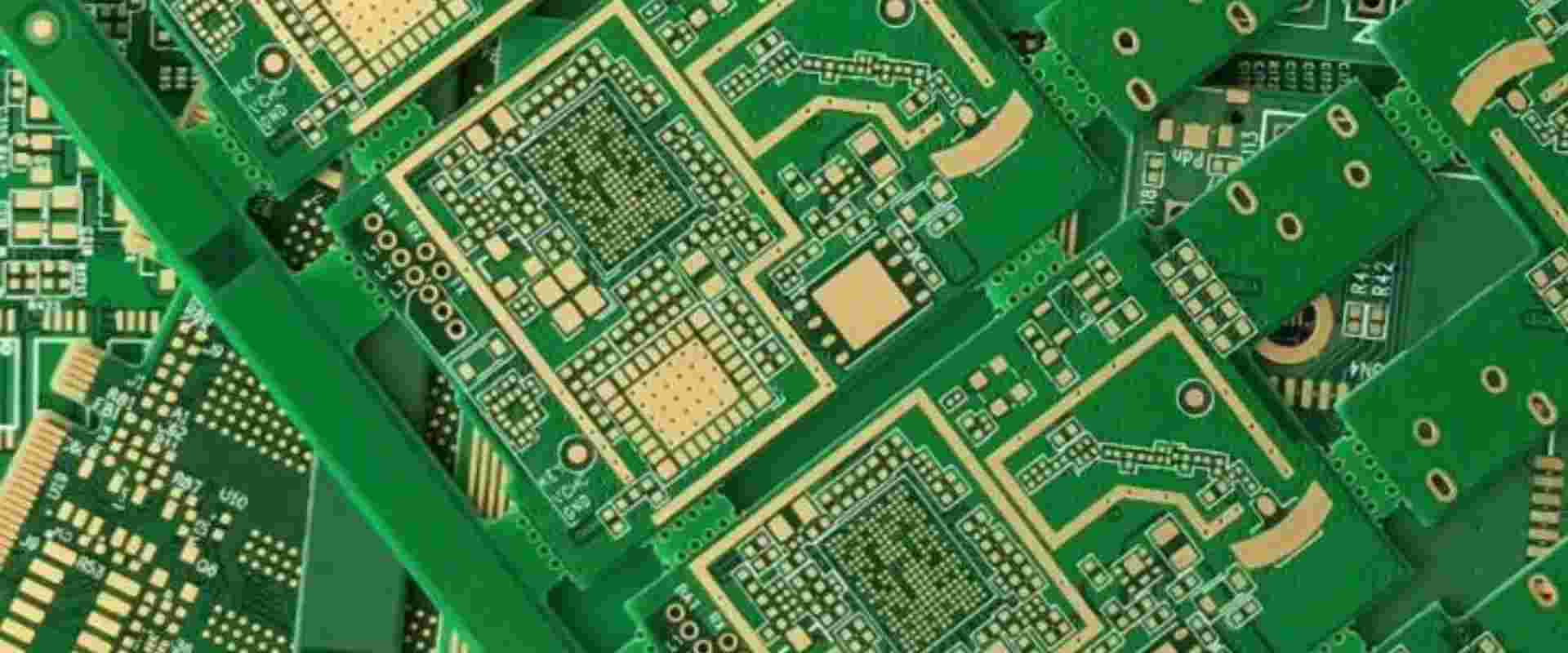
FR-4 is a widely used material in the electronics industry for producing printed circuit boards (PCBs). It is an epoxy resin that has been reinforced with glass fibers and provides superior strength, durability, and heat resistance when compared to other PCB materials.
FR-4 also offers excellent dielectric properties, making it ideal for use in high-voltage applications. The unique blend of these features makes FR-4 one of the most commonly chosen materials when creating complex electronic devices.
The composition of FR-4 gives it its unique characteristics, allowing for custom designs and flexibility in product development processes. Its combination of pliability and rigidity allows engineers to create complex circuitry without worrying about flexing or breaking during operation.
Furthermore, the inherent flame retardant property ensures that any accidental sparks or overheating will not ignite nearby components or cause additional damage to the board itself. In addition to being extremely versatile, FR-4 can also be machined into various shapes with ease due to its relatively low melting point.
This makes it possible to fabricate intricate components onsite rather than relying on expensive offsite production methods like injection molding or etching techniques. For example, microcontrollers can easily be soldered directly onto a prepared surface using standard tools such as hand drills and hot air guns instead of more specialized machinery which may be required for some projects involving other types of PCBs.
Overall, understanding how FR-4 works is key for anyone involved in designing printed circuit boards because knowing its strengths and limitations helps determine whether this material is suitable for their specific application requirements before investing too much time into development costs associated with alternative solutions.
Advantages of FR-4 for PCBs
FR-4 is one of the most widely used materials for printed circuit boards (PCBs). It offers several advantages, making it an ideal choice in many PCB applications.
The first advantage is that FR-4 has excellent electrical insulation properties. This makes it suitable for use in circuits where there may be high levels of electrical current or interference.
Additionally, FR-4 also has great mechanical strength and thermal stability, making it resistant to temperature changes and other environmental factors which could impact its performance. Furthermore, with proper dielectric treatments applied to FR-4 boards, they can even reach greater levels of resistance against voltage surges and EMI/RFI noise from electronic components nearby. Aside from its physical features, another major benefit of using FR-4 material over other materials is its cost-effectiveness.
Not only are the raw materials relatively inexpensive but so too are the manufacturing costs associated with producing PCBs made out of this material – both due to its low requirement for manual labor as well as the fact that fewer layers need to be built up during production compared with other substrates such as ceramic or polyimide ones. Finally, since FR does not require any special treatment after manufacture either when soldering or protecting against moisture ingress; overall maintenance costs can remain low throughout the product’s lifetime which helps ensure maximum possible cost savings for manufacturers looking to cut down on their expenses without compromising quality standards at all times.
Considerations When Choosing FR-4

When it comes to choosing FR-4 for making Printed Circuit Boards (PCBs), there are a few important considerations. First and foremost, the environmental conditions of the application should be taken into account since certain temperatures or chemicals can affect the properties of FR-4 material.
Additionally, flame ratings should also be considered based on their UL 94 V rating which denotes the level of flammability. The thickness and copper weight (oz) of the board is also important factor that needs to be considered since this will determine its overall strength and durability in various scenarios.
Furthermore, one must consider the cost associated with using FR-4 as compared to other materials available in the market such as Polyimide or polyester laminates, etc., depending upon specific requirements.
Ultimately, selecting an appropriate grade of FR-4 material within budget while meeting all design criteria is key when deciding on a PCB construction material.
Conclusion
FR-4 is a widely used material for PCBs and has proven to be incredibly useful due to its high strength and flexibility. Its versatility, cost, and widespread availability make it an ideal choice for many applications in the electronics industry.
It offers excellent electrical insulation properties, making it suitable for use with high-frequency signals while remaining relatively inexpensive compared to other options. FR-4 for PCBs is also flame retardant which adds an extra layer of safety that can help protect against potential fire hazards. All in all, FR-4 is a great option for PCB fabrication as it provides long-lasting performance while being affordable and safe.